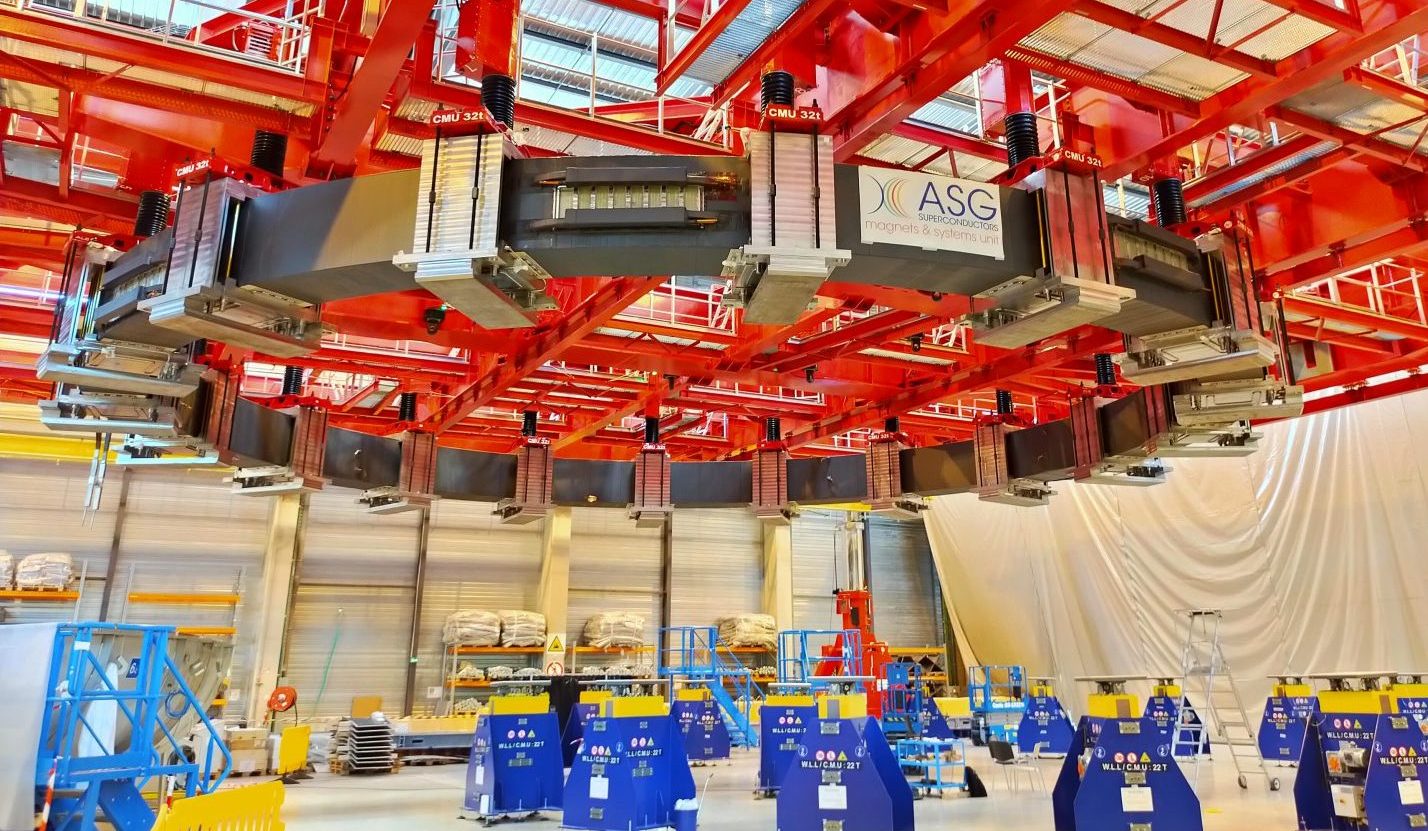
Due to their exceptionally large dimensions, four of the six poloidal field coils that will be installed in the ITER machine cannot be produced off site and shipped, and therefore have to be manufactured in the Poloidal Field Coils Winding Facility, a factory set up on the ITER site in Caradache, France. Fusion for Energy (F4E), the European Domestic Agency, is in charge of procuring five of these magnets, and manages the Poloidal Field Coils Winding Facility and the contractors involved in their fabrication.

After the selection of a number of contractors, F4E has furnished the manufacturing facility with tooling in order to perform qualification and production operations. Sea Alp, Criotec, Elytt Energy, Alsyom, and Seiv have supplied the tooling, ASG Superconductors is acting as engineering integrator, and CNIM along with ASG are in charge of manufacturing.
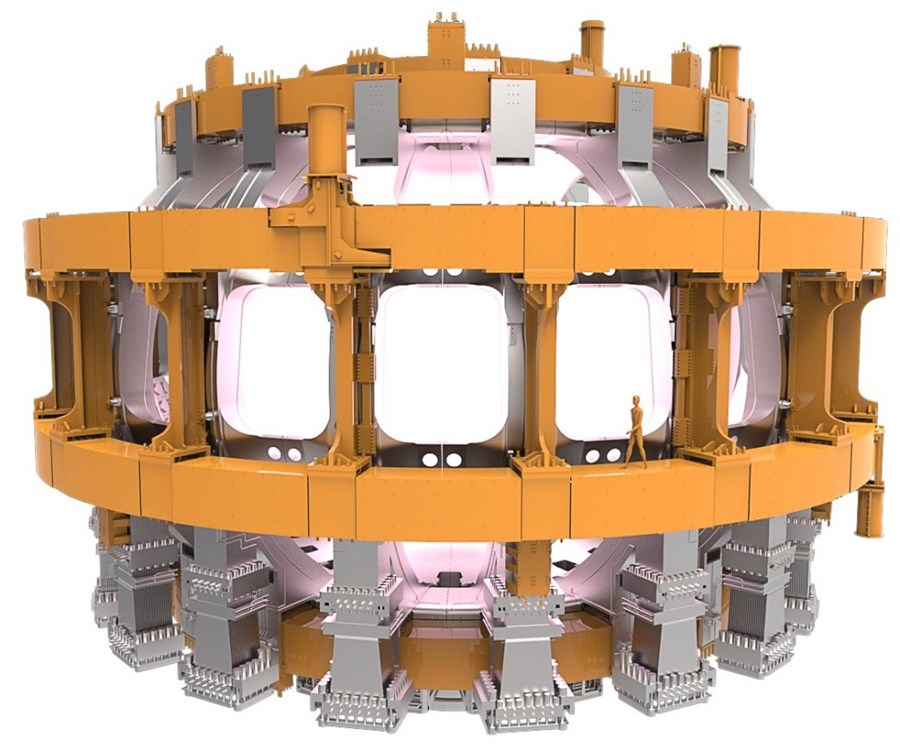
The poloidal field (PF) magnets are six ring-shaped coils situated outside the toroidal field magnet structure to control the plasma shape and stability by “pinching” it away from the walls. Six of these powerful magnets, with diameters ranging from 8 to 24 meters and weighing between 200 and 400 tonnes, are wound using NbTi superconductor and will be installed in ITER reactor. PF coils are made of six to nine circular conductor arrangements, called double pancakes, that are insulated, resin-impregnated, stacked together and compressed.
- PF1: 8 meters diameter, 200 tonnes, 8 double pancakes.
- PF2: 17 meters diameter, 6 double pancakes.
- PF3: 24 meters diameter, 8 double pancakes.
- PF4: 24 meters diameter, 8 double pancakes.
- PF5: 17 meters, 340 tonnes, 8 double pancakes.
- PF6: 8 meters, 400 tonnes, 9 double pancakes.

PF6 is the second smallest of the ring magnets in terms of diameter, but the heaviest coil (400 t) and the first that will be inserted in the ITER pit. It has been produced in China through a collaboration between F4E and ASIPP, the Institute of Plasma Physics of the Chinese Academy of Sciences. PF6 is the first poloidal field coil to be completed and arrived at the ITER site last June. The coil will now go through inspections, dimensional checks and cold tests which are foreseen to last from two to three months.
PF5 is the first coil to be produced by European contractors in the on-site F4E winding facility. After undergoing impregnation, painting and dimensional checks, PF5 is currently in the final assembly phase.

In the meantime, PF2 has been ground insulated and will go through impregnation which is expected to last around three months. Since it has the same diameter as PF5, PF2 fabrication is benefiting from lessons learned with PF5 and the coil is being manufactured on the same tooling.
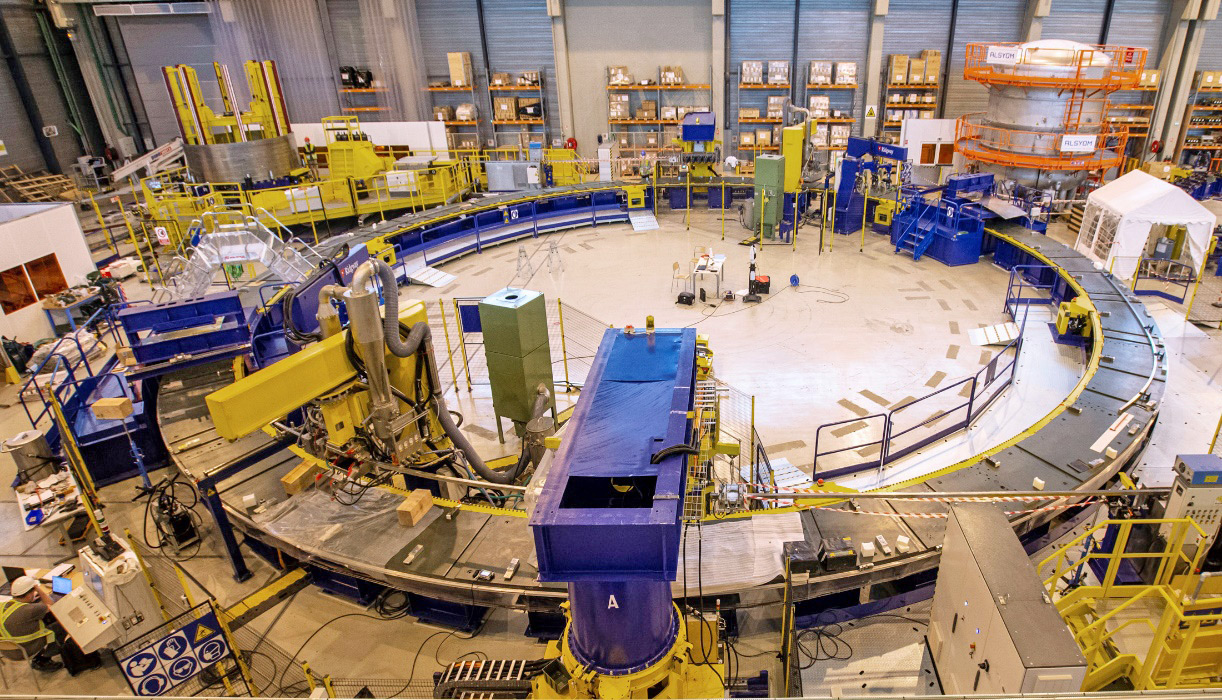
The teams are now getting ready for the production of PF3 and PF4, which are much bigger coils (ø24 m). The winding station, where the conductor will be wound, has been reconfigured and the tests with a dummy conductor have already started.

Source: F4E.